
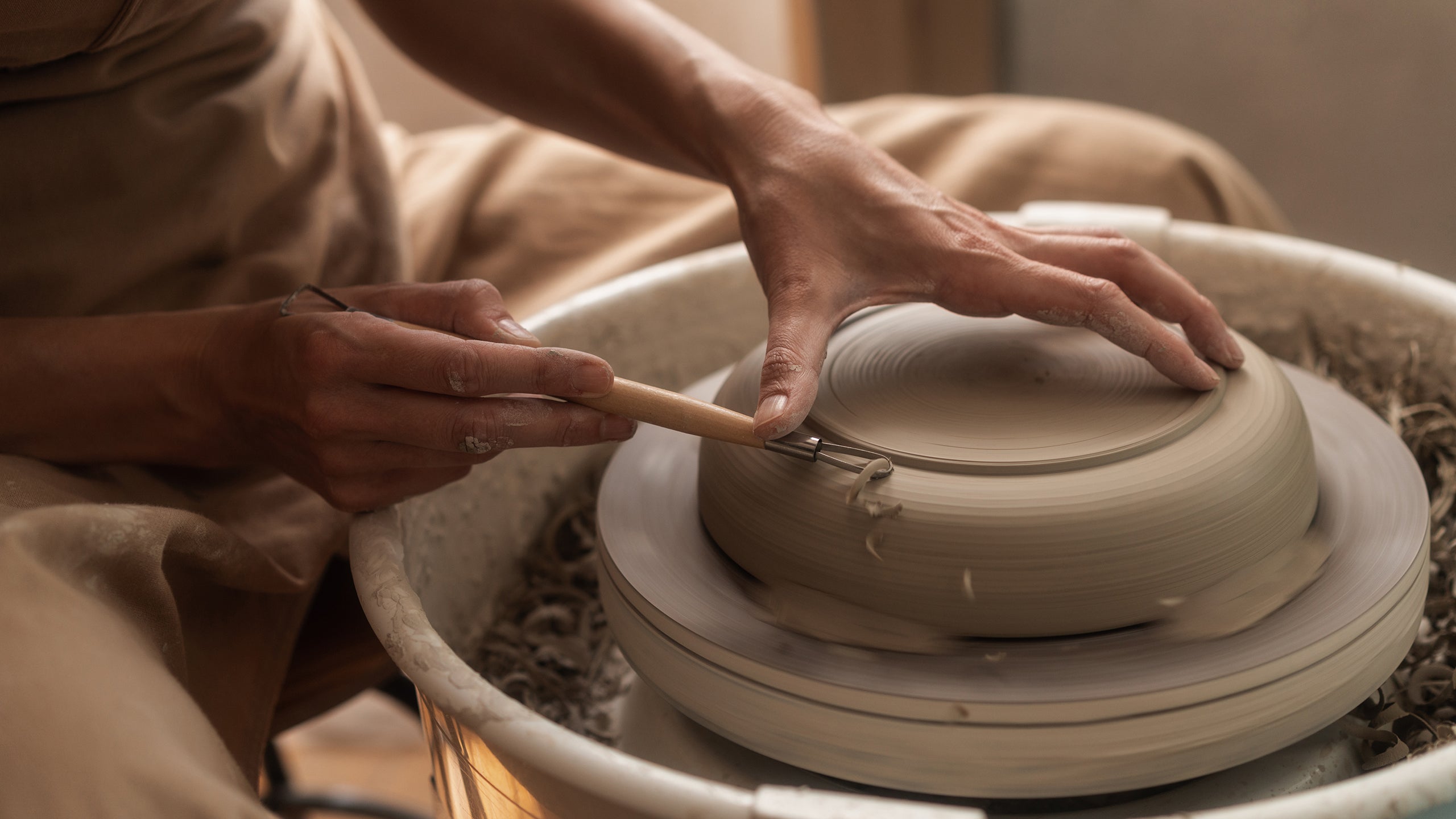
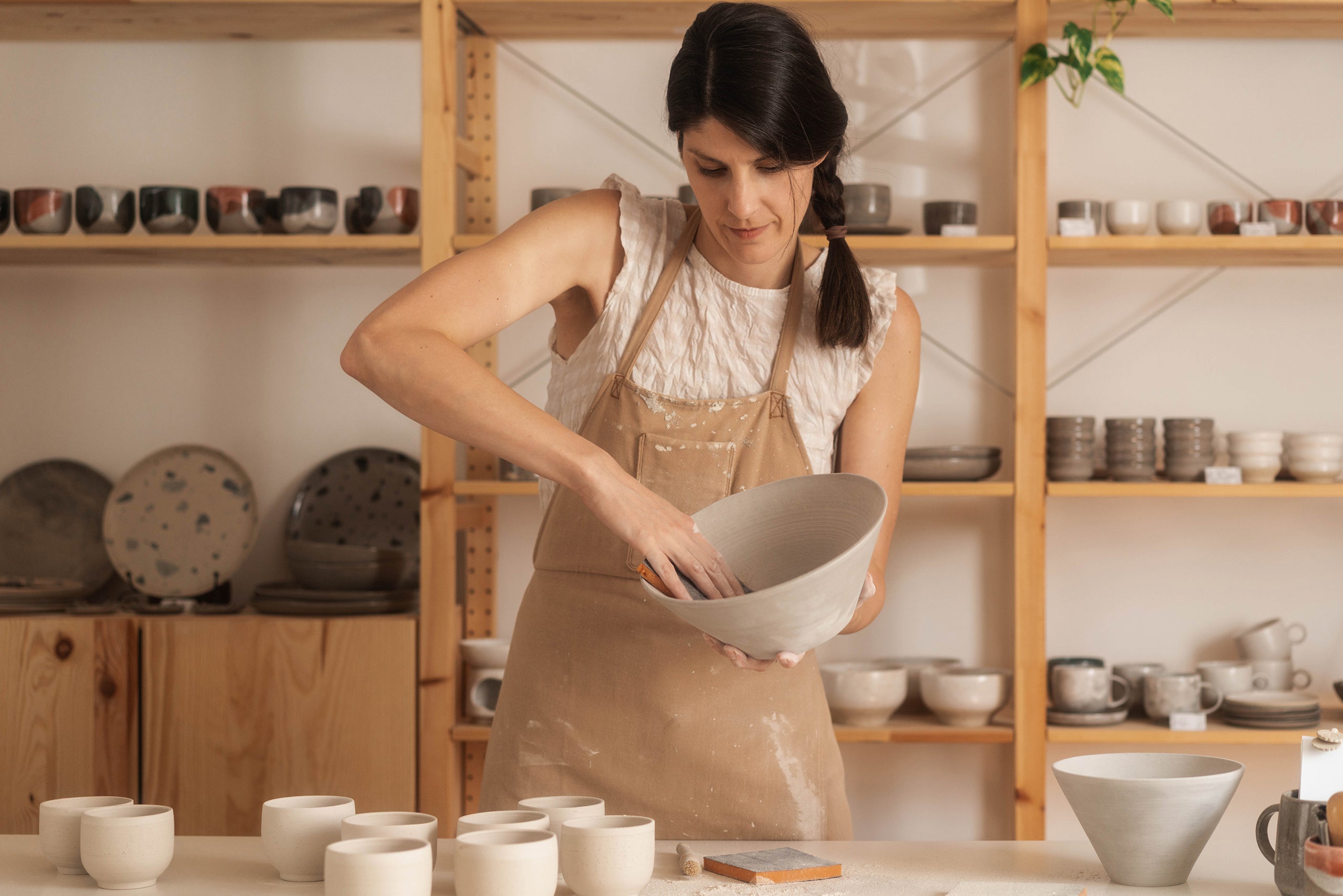

Introducing
Our Creative Process
We find great pride and inspiration in our creative process, which typically spans 2-3 weeks from the initial shaping to the final glaze firing stage. The timeline can vary based on the size and complexity of each individual object. Below, we've outlined all the steps involved in this intricate process:
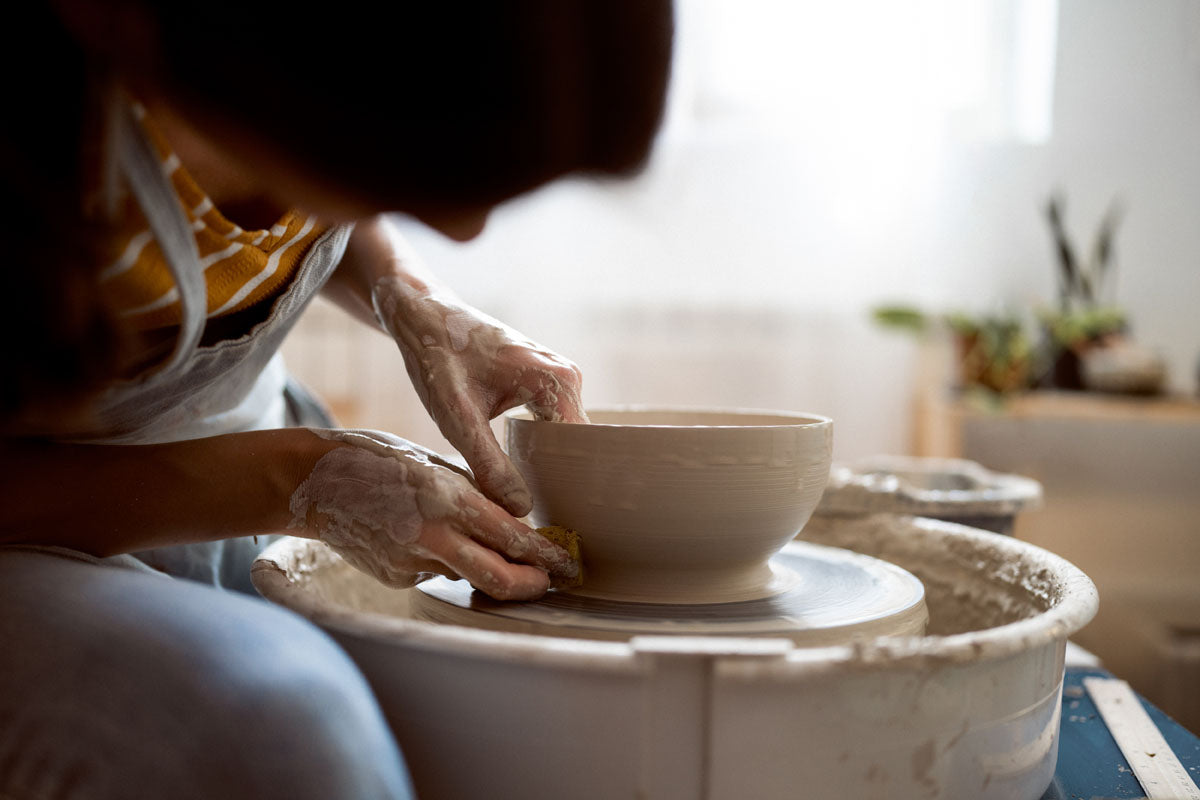
STEP #1
SHAPING ON POTTER’S WHEEL / THROWING
Each piece is shaped on a potter’s wheel, using only hands and the essential tools, such as sponges, wooden pottery knives and ribs... We use high quality clay, predominantly in earthy tones, with high concentration of clay grog – speckled cream, gray, black, terracotta, and sometimes even a mix of 2 or more clay bodies.
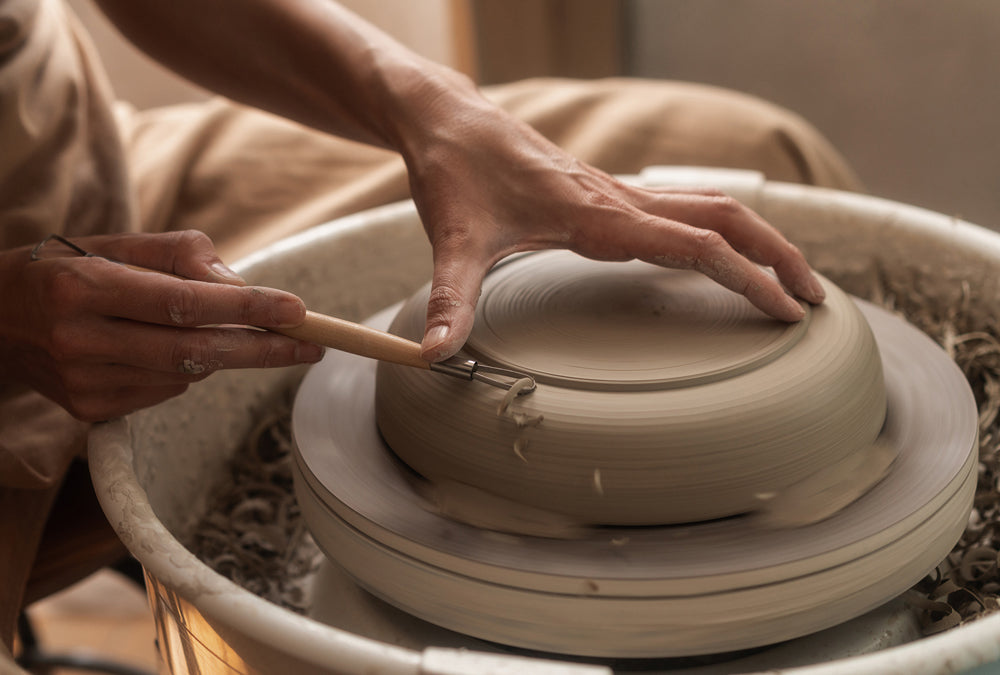
STEP #2
TRIMMING ON POTTER’S WHEEL
After throwing, we let the pots sleep under a plastic bag overnight and continue working on their form the next day. By stripping off any excess clay with metal pottery tools, we form a small foot, which makes our ceramics lightweight and reduces the total area of contact with table surface, preventing scratching and damage of your furniture.
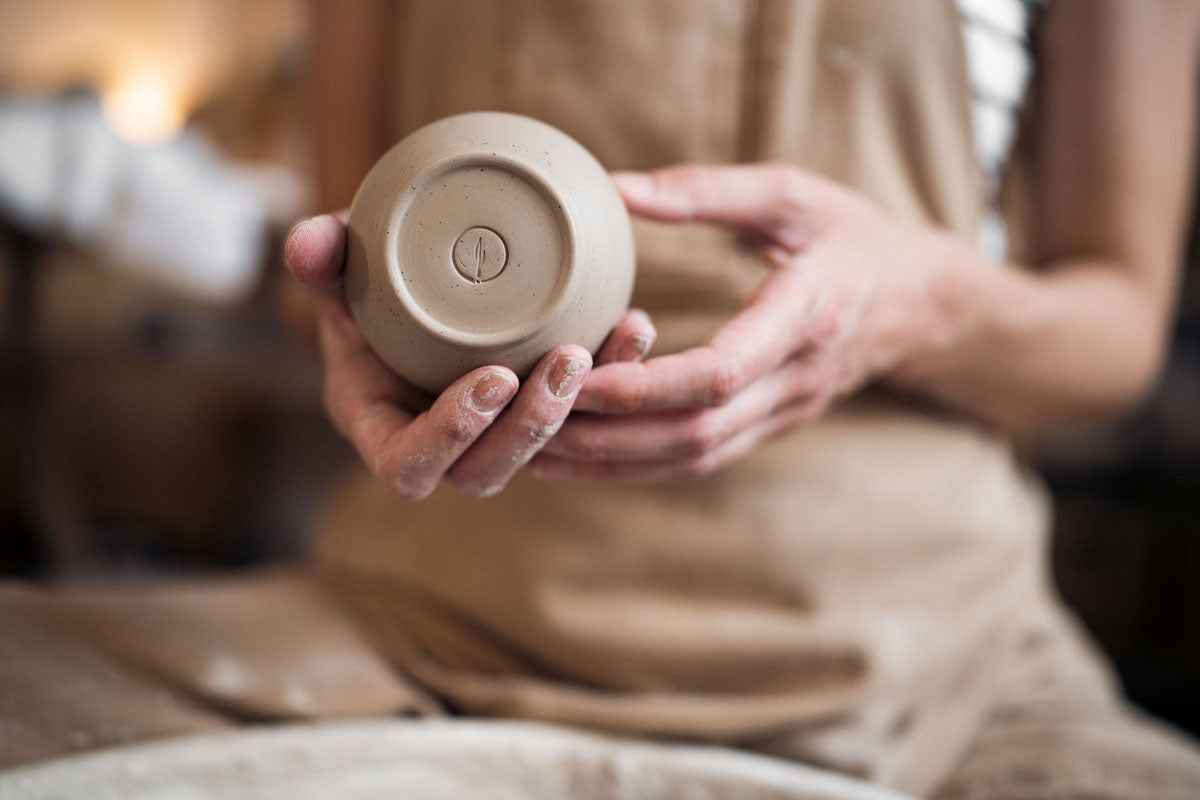
STEP #3
DRYING
Drying takes from 3 to 10 days, depending on the size and complexity of an object. We try to slow down drying time by covering our leather hard pieces with plastic bags, because fast and uneven drying can result in warping and cracks.
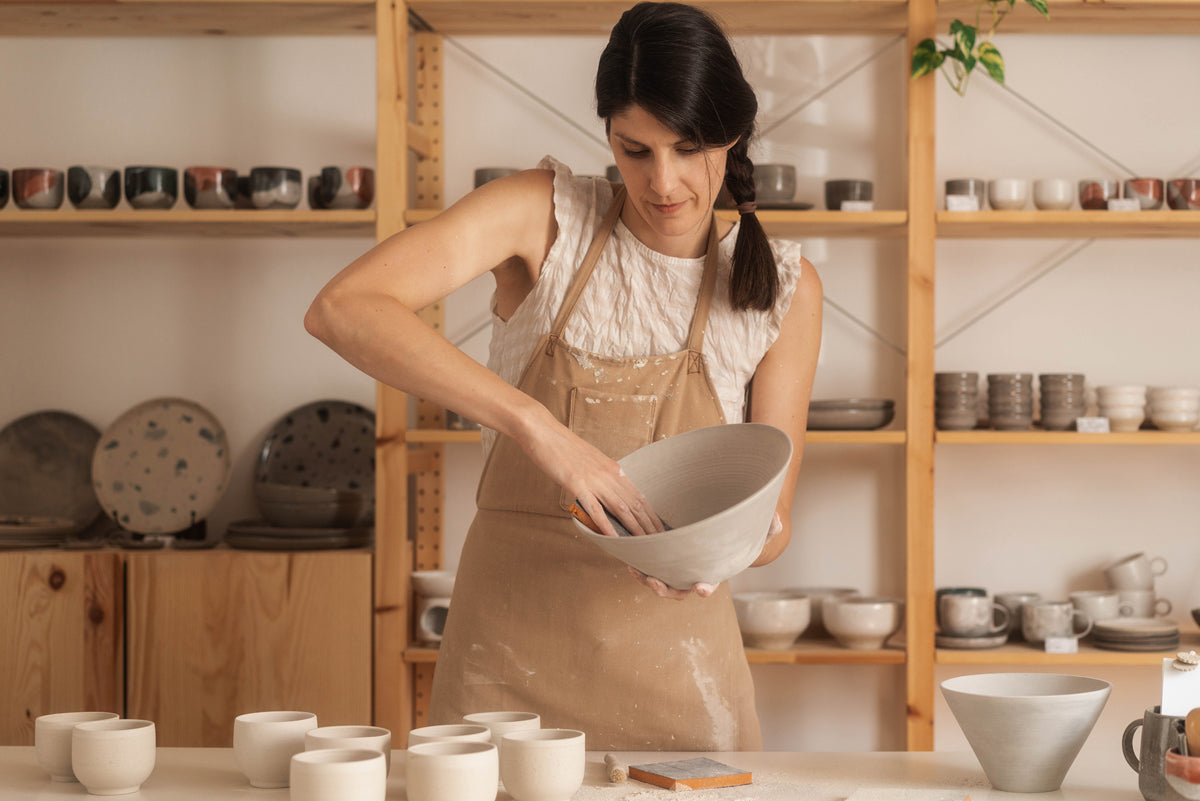
STEP #4
SANDING
After drying, ceramics go through a minor sanding, which smoothens rough surfaces and eliminates any sharp edges, concluding the first major part of pottery making. The ceramics have now reached their greenware stage and are ready for the bisque firing!
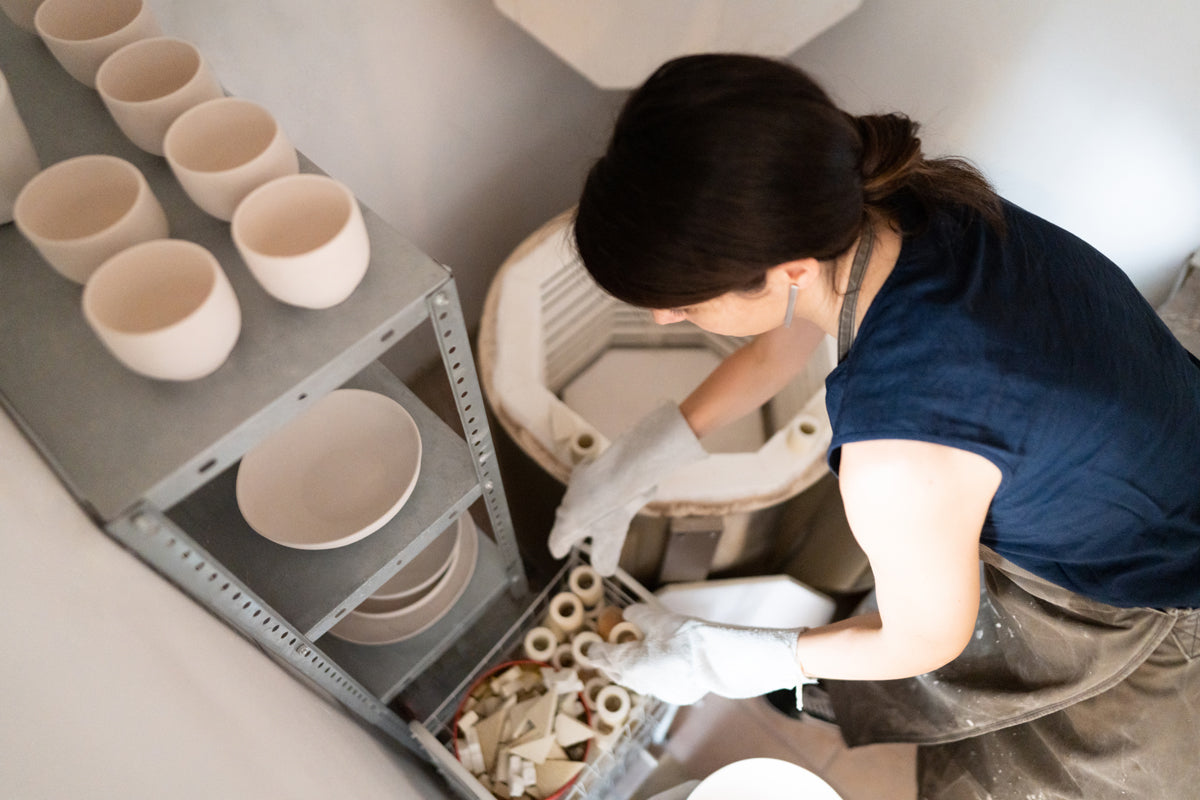
STEP #5
BISQUE FIRING
Still highly fragile, unfired ceramics are carefully placed into the ceramic kiln. They are fired at 850 deg, leaving the kiln after 24h, porous but firm enough to be held and handled during the glazing.
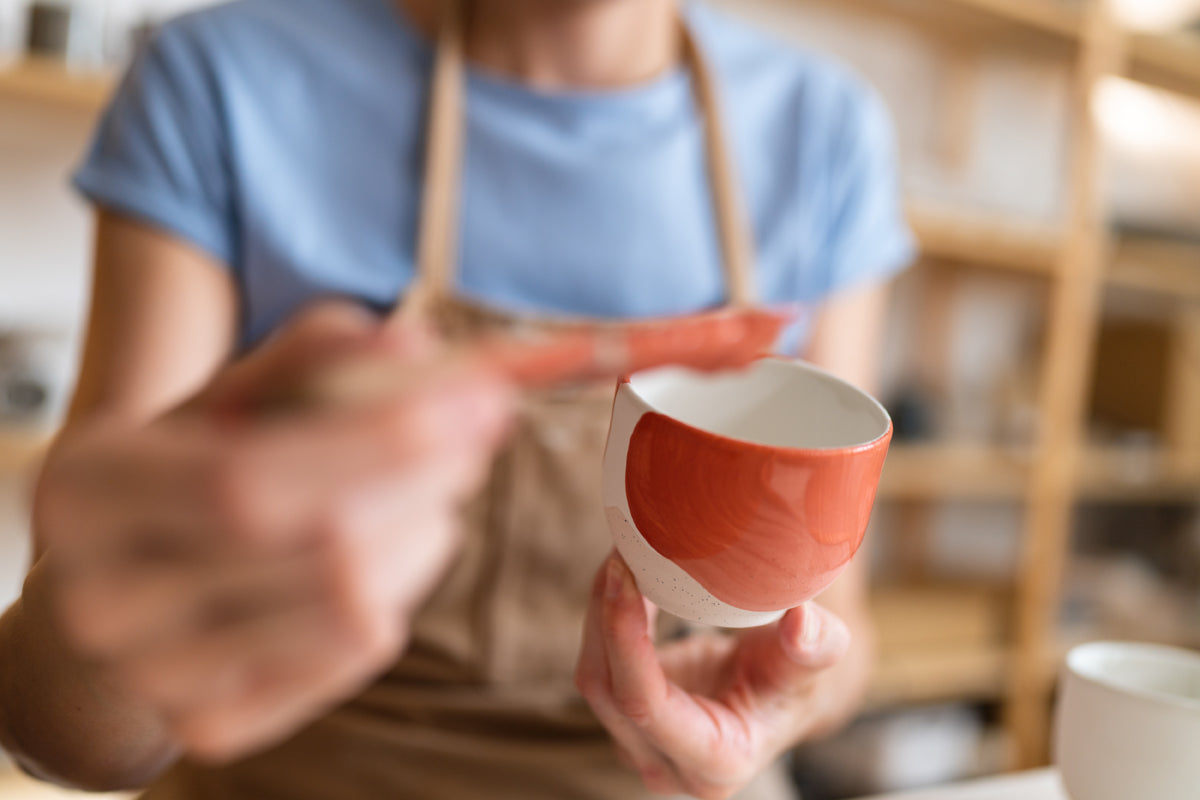
STEP #6
GLAZING
Bisque fired pieces are often dusty and they have to be wiped by a damp sponge, or sometimes washed before the glaze application. It is essential to let them dry well after cleaning in order to ensure good absorption of glaze into the bisque.
We use two types of glazes, so-called dipping glazes for our Speckled White series and brush-on glazes for our Sand and Artsy series. Brush-on glazes are applied in 2 or 3 thick layers by special glaze brushes. They give the best results when intentionally overlapped in two or 3 different tones. This is the technique of glaze layering and it’s our favourite method of glaze decoration, best displayed in our Artsy series of cups.
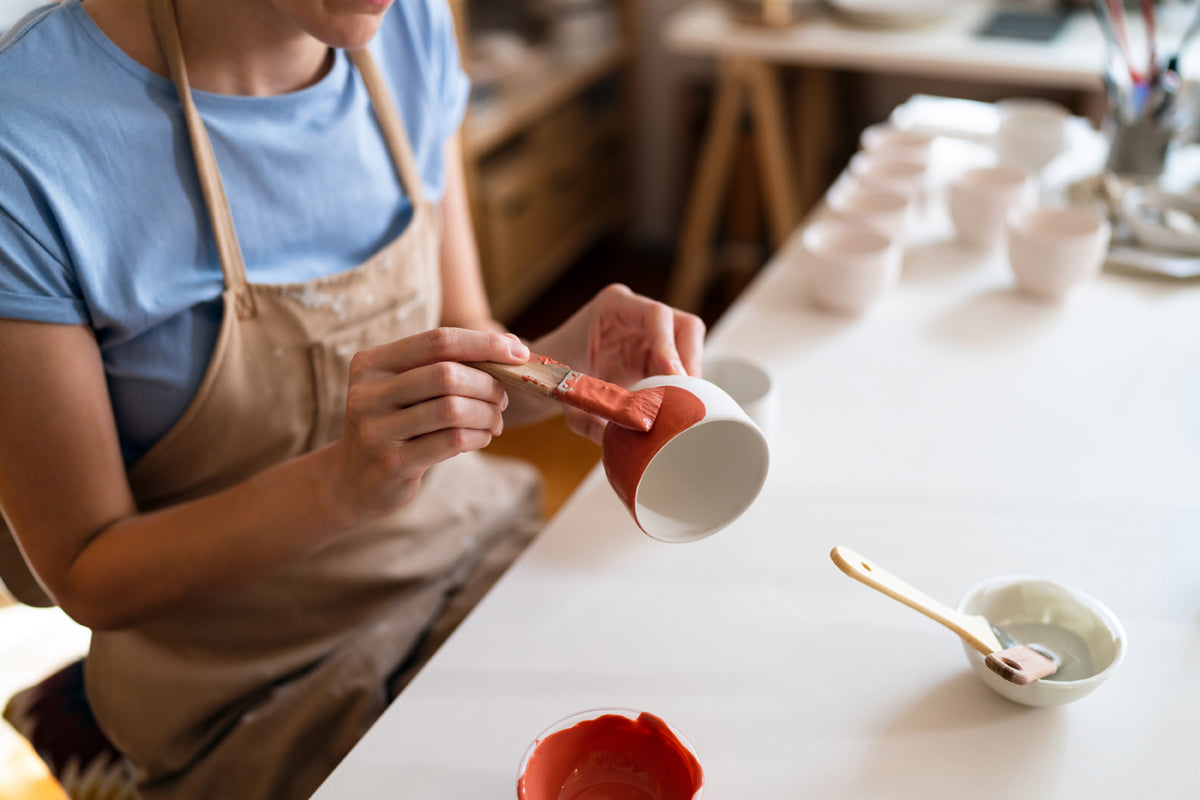
STEP #7
GLAZE FIRING
The final step in our pottery making process is glaze firing at 1220 deg, during which the glazes melt, forming a glasslike surface. Ceramics fired at temperatures over 1200 deg are called stoneware. They are highly durable and resilient. During firing, glazes change their tone and often create wonderful melting-like effects inside the kiln. This is why we say most of the magic happens during the glaze firing, when all elements come together - earth, water, air and fire. Glaze and clay become one, bringing to life a new functional object. Two days later, once the fired batch cools down, we unload the kiln, grind the bottoms to flatten any irregularities and ensure smooth surface of unglazed parts.
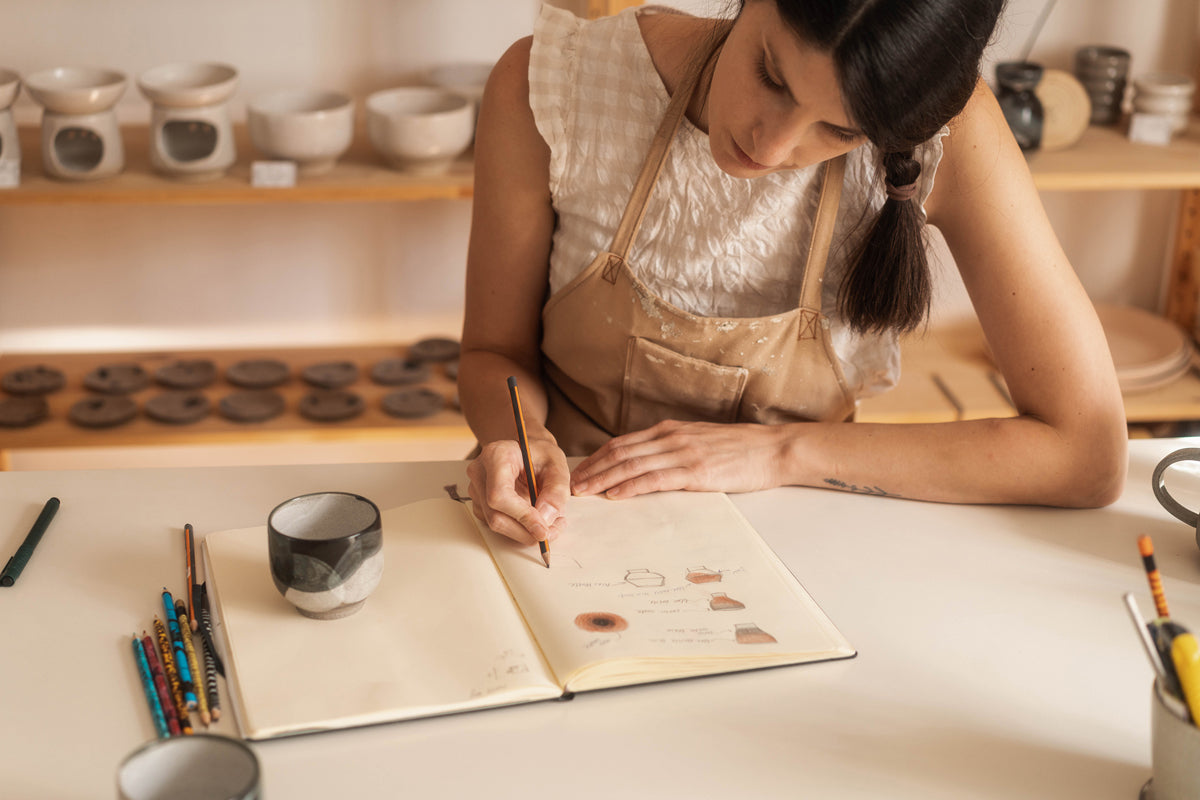
STEP #8
DOCUMENTING
We usually photograph finished pieces in-house, before we drop them to our online shop. Taking and editing photos is an essential part of our process. While arranging pottery and always shifting camera angles we get to see finished products in various compositions and perspectives, taking mental notes on the possible improvements and future developments. Often an idea for a new product or finish pops in our mind during the photo shooting!
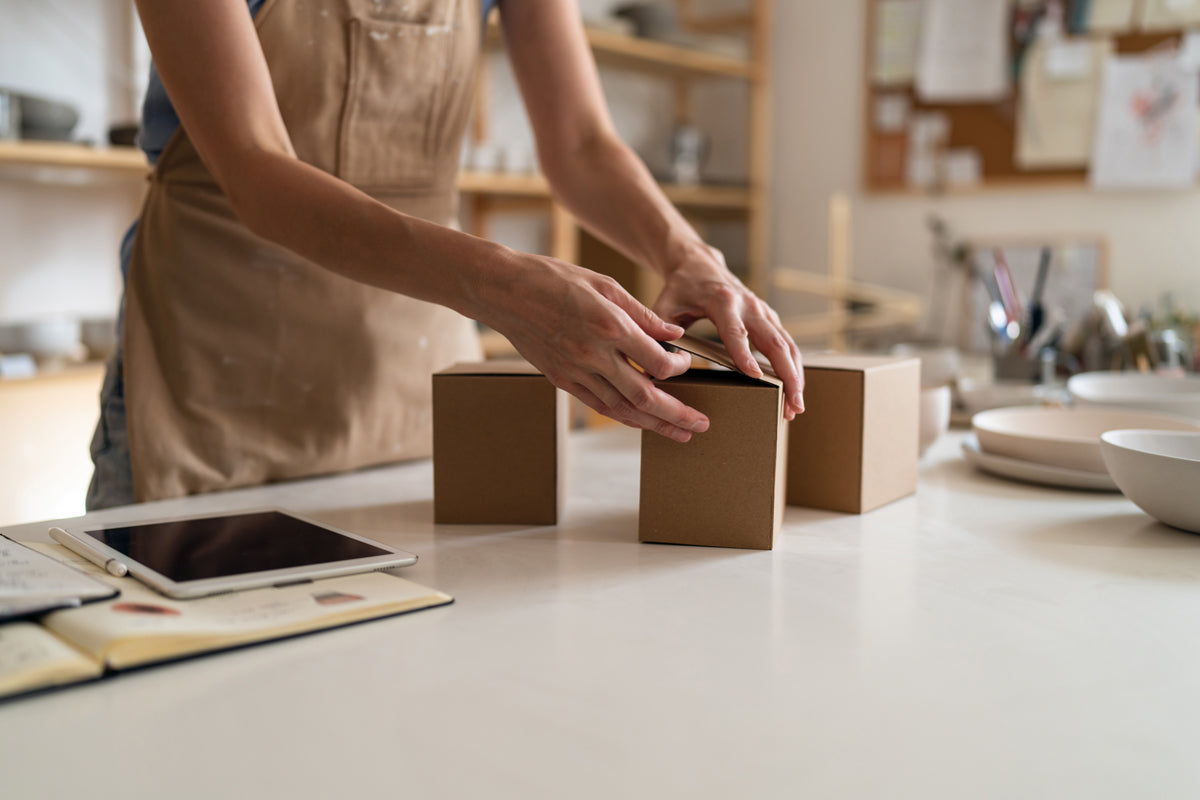
STEP #9
PACKING
Due to their delicate nature, all of our ceramics are carefully packed in crafty eco-friendly packaging.
We put a lot of effort into securing each pot with multiple layers of paper and protective cardboard within a double-box packing system we have established over time, to prevent any potential damages and breaking.
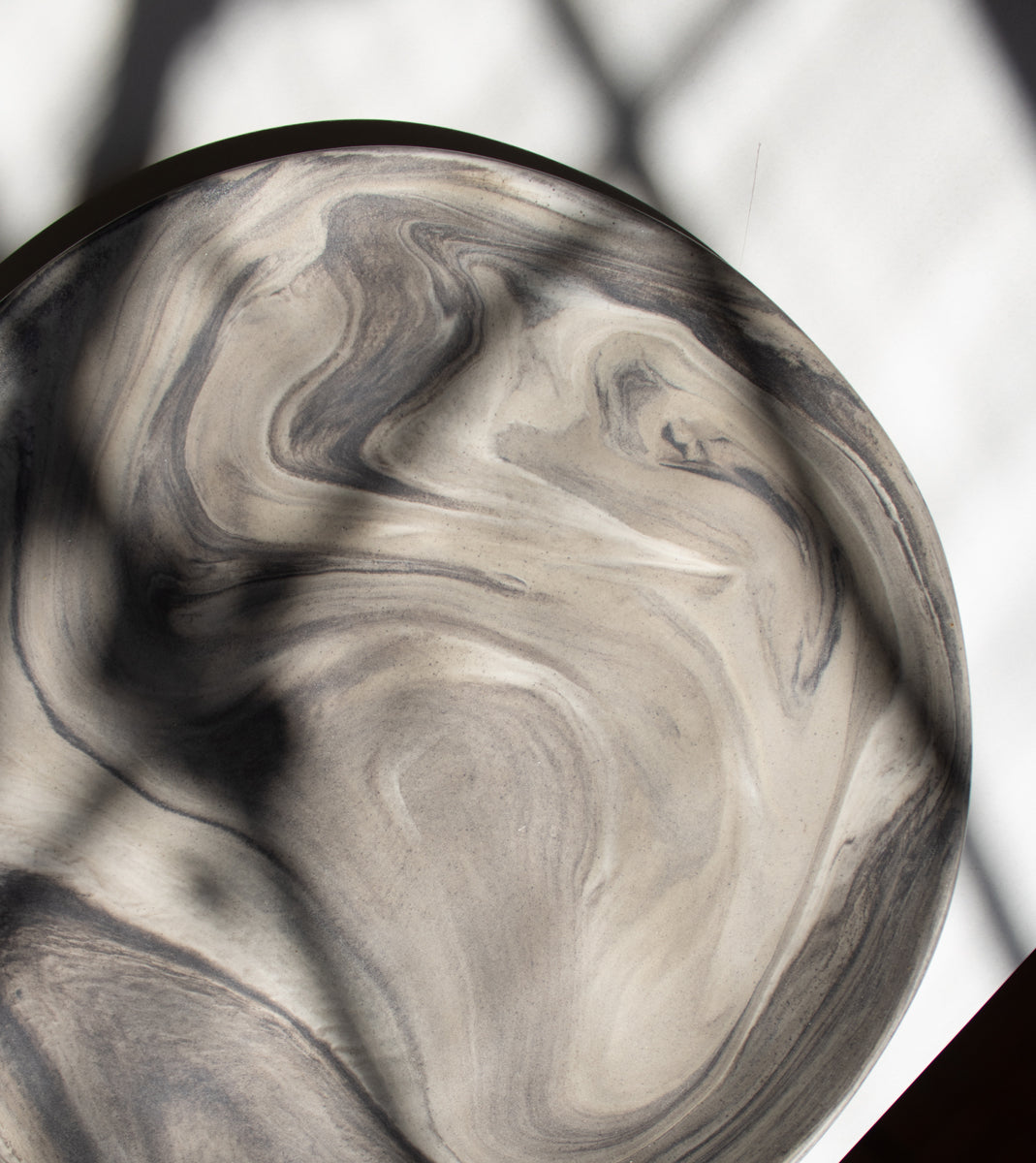
when they reach their new home
SAFETY & CARE
Safety and durability of our ceramics take precedence. All our products are food and drink safe. They are glazed with lead-free glazes and fired at high temperatures (1220C), which makes them extremely resistant and durable. Made of Dust ceramics dishwasher and microwave-safe.
Avoid exposing very warm ceramics to extremely cold water, or pouring very warm liquid into previously fridged ceramics. Glazes we use will not retain oil stains. However, in rare cases, unglazed parts of our ceramics may get stained over time. These stains can be removed with rough side of a sponge and baking soda/vinegar.
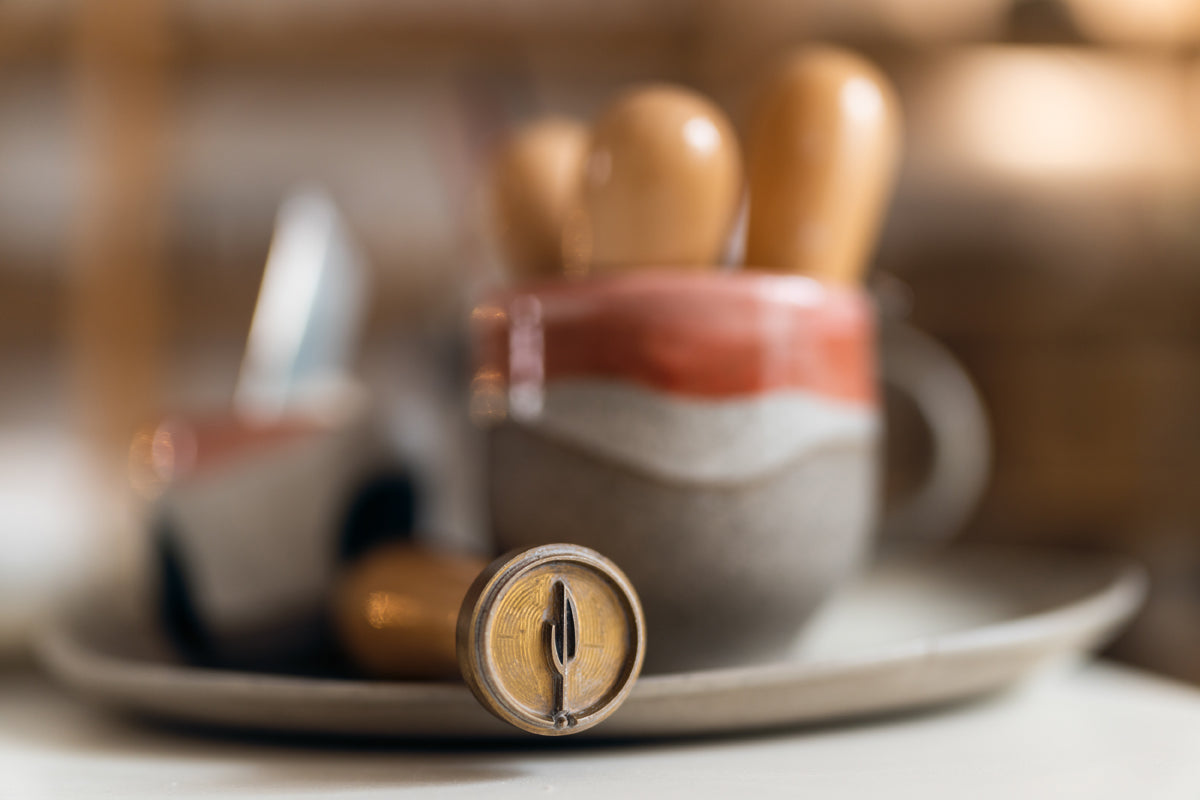
more to love
SECONDS AND SAMPLES
On rare occasions, a piece will develop a minor flaw at one stage in the process – a hairline crack, glaze that is too thick or thin, warped surface, over or under crystallized glaze...We periodically offer these “flawed” pieces at discounted prices, as there are always people who happily give them a home, adding them to their collections. Although most of these pieces are highly functional, we call these pieces SECONDS and they are always placed in a separate section at our web-shop. Within this section, you can also often find fully functional unflawed items from older collections, as well as some samples developed for a potential collaboration or an internal studio project. Each piece is marked as „second“ or „sample“, depending on it’s characteristics, to describe the type of distinction from a standard full-priced product.